This is an editable PowerPoint four stages graphic that deals with topics like business process improvement tools to help convey your message better graphically. Business Process Improvement can work in two ways.
Ppt Using Process Management Tools To Strive For Continuous Improvement Powerpoint Presentation Id 6127383
Presenting this set of slides with name business process improvement tools ppt PowerPoint presentation show graphics cpb.
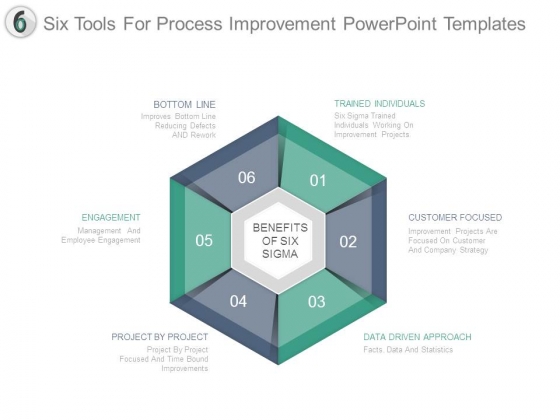
Tools for process improvement ppt. Business Process Design Business Strategy Core Process Prepare Management Commitment Sponsorship Align with Strategic Goals Team Organisation Current Process AsIs Review Current Process Review Key Performance Data Identify Process Customers their Needs Future Process ToBe Vision Scope Targets for Future Process Benchmark Best practice. Having a structured approach to how you brainstorm increases the quality and efficiency of your efforts. Seven tools of quality The Old Seven The First Seven The Basic Seven Quality pros have many names for these seven basic tools of quality first emphasized by Kaoru Ishikawa a professor of engineering at Tokyo University and the father of quality circlesStart your quality journey by mastering these tools and youll have a name for them too.
Continuous improvement found in. It is further shown how to involve 7QC tools in some phases of continuous improvement Process PDCA-cycle Six Sigma DMAIC and Design for Six Sigma DMADV methodologies and Lean Six. ICOR inputs outputs controls and resources is an internationally accepted process analysis methodology.
Historical and Definition of Enterprise Quality Managing Service Level Agreements SLAs Final Projects activity. Lets know how smaller changes in life can become a huge part of your self-growth. Six Sigma Statistics Training Powerpoint.
Depending on the project scope the team might hold off on the process flowchart and Gage RR activities until primary focus areas are identified further into the project. PFMEA Training PPT DMAIC Tools. The process below gives you that structured approach.
The approach and tools described in the handbook follow a Basic Process Improvement Model. It aims to eliminate all waste from process flows to achieve a. Strongly recommend Six Sigma Certification to gain a full understanding of these tools and how they fit into the DMAIC process.
We can construct a dynamic model - a picture of the activities that take place in a process. Brainstorming is a structured process to capture a groups ideas relating to a topic or issue. Project Ideation activity Day 2.
Process maps are useful communication tools that help improvement teams understand the process and identify opportunities for improvement. Together with the Basic Tools for Process Improvement or tools kit it provides the practical information you need to initiate and successfully carry out process improvement activities. The audit is usually the best place to start process improvement efforts.
If you have finally made your mind to think high and act high you can also take a self-improvement course. Improving Service Quality With Lean Process Tools1 2. Process Improvement Other Tools for Process Improvement Kaizen Blitz Poka-Yoke Process Simulation Key Idea.
Total Quality Management TQM. Here are some of the things you can practice to evolve in the process of self-improvement. Quality Improvement Is used to make improvements to a process Focuses on making an entire systems outcomes better by constantly adjusting and improving the system itself instead of searching out and getting rid of bad apples Think of ways you try to improve your own processes everyday.
If you use it you wont waste your participants time and youll get a lot of great ideas. Whether its caring for your. Lean Process Improvement Techniques 1.
Some of the important tools in this phase include trend charts basic Pareto charts process flowcharts Gage RR and process capability measurement sigma level also referred to as process sigma. Sample Of Five S Continuous Process Improvement Powerpoint Slide Background Picture Continuous Improvement Vs Process Improvement Ppt Slides Culture Of Continuous Improvement Example Of Ppt. Download Process Improvement PowerPoint templates ppt and Google Slides themes to create awesome presentations.
Process Improvement Tools and Templates Menu. A data-driven approach to reduce defects to improve an organizations performance. A kaizen blitz is an intense and rapid improvement process in which a team or a department throws all its resources into an improvement project over a short time period as opposed to traditional kaizen applications which are performed on a part-time basis.
A systematic process to minimize waste without sacrificing productivity. It can flow through a structured path or take a more informal route. Presentation of proposed Final Term Project CharterDay 3.
A process improvement methodology born in Japan kaizen espouses the idea that business improvement is continuous and never ending. Know when and how to apply the basic tools of improvement to various problems and analyses Be able to make more informed decisions based on facts and data Understand how to determine if a process is in control and capable. Features of these PowerPoint presentation slides.
Lean Process TT Tools and TechniquesFinal Projects activity. Identify work as a process with inputs and outputs. Free Easy to edit Professional Lots backgrounds.
Involved in process improvement efforts. How Process Improvement Works. A combination of Lean and Six Sigma methodologies.
An organization-wide effort focused on continuous improvement to improve. Process Audits And Finding Improvement Opportunities. PowerPoint PPT presentation free to view.
Either way though it tends to follow four common steps. Heres an article on Six Sigma. Six Sigma DMAIC.
Continuous improvement can range from simple projects where its a case of just do it or they can be longer-term projects. Lean six sigma is the combination of two different concepts combined together to form a powerful tool to improve business processes Over the last few decades companies all over the world have saved countless millions by incorporating Lean and Six Sigma strategies into their processes.
Continuous Improvement Tools And Techniques A Practical Guide For Improving Quality Productivity And Performance In Organizations Johnson A Edosomwan Dsc 9781879849006 Amazon Com Books
From DMAIC to root cause analysis and beyond these are the core tools and techniques which drive sustainable change.

Continuous improvement tools and techniques. One of the most popular process improvement tools is the Plan Do Check Act cycle PDCA. Relies on many lean tools such as Continuous Flow Heijunka Kanban Standardized. Other techniques that are part of the continuous improvement arsenal are the Gemba walk and the A3 report.
Here are the top 9 Lean and Six Sigma process improvement techniques including 5S Kaizen DMAIC DMADV value stream maps process maps BPMN and more to help you streamline your business processes. Using and Leveraging the right one can lead to improved productivity less waste reduced costs and errors and greater profitability overall. The DMAIC improvement cycle is an effective technique for structured change management.
A strategy where employees work together proactively to achieve regular incremental improvements in the manufacturing process. This is done surprise surprise by periodically examining and improving your processes to smash bottlenecks use the best software and take advantage of the most efficient methods. If you already have a good basic understanding of process improvement as a methodology jump ahead to the first tool Drive.
The A3 report is a structured approach that helps you deal with problem-solving issues while the Gemba walk encourages you to go and see where the real work happens. You will learn how continuous quality improvement is part of a hospitals culture how it benefits a healthcare organization and about one of the most popular methods of implementing CQI. Continuous Improvement Tools List.
In this paper a review of possibilities of the systematic use of. William Edwards Deming and Walter Shewhart. Continuous improvement tools and techniques are a powerful resource in the lean manufacturing implementation programme.
Heres an overview of the six most popular and effective continuous improvement tools available. Before we dive into the specific tools lets talk basics. These steps are used to help ensure that improvements are data-driven measurable and repeatable.
This four-step model is often shown as a circle because continuous improvement is a process that should be repeated over and over again. Problem solving methodology such as DRIVE Process mapping Process flowcharting Force field analysis Cause effect diagrams CEDAC Brainstorming Pareto analysis Statistical process control SPC Control charts Check sheets Bar charts. The PDCA cycle short for plan do check act provides you with a systematic approach to testing different ideas and hypotheses.
The PCDA Cycle to systematically test hypotheses. There are a number of tools available to ensure that continuous improvement is successful which include. Continuous need a deeper analysis but it is evident that 7QC improvement PDCA-cycle Six Sigma and Design tools have a big role in all the key phases of these for Six.
The PDCA cycle short for plan do check act provides you with a systematic approach to testing different ideas and hypotheses. It can help you to implement continuous improvement throughout your organization using a structured framework. Then try these continuous improvement tools and techniques.
If organizations to achieve continuous quality improvement they need to use appropriate selection of quality tools and techniques. Continuous Improvement What is Kaizen. Heres an overview of the six most popular and effective continuous improvement tools available.
Convert setup steps to be external performed while the process is. DMAIC is a project methodology with five phases. Working together a group of people involved in a process are able to think more freely building on each others ideas to identify and explore all the possible.
A3s to provide vision and structure to big-picture improvements. It includes practical application of Quality management processes and tools are presented for the continuous improvement of organizational quality. The tools and techniques most commonly used in process improvement are.
As weve already mentioned continuous improvement means constantly improving your processes. It can help you to implement continuous improvement throughout your organization using a structured framework. Brainstorming can be a useful aid when using continuous improvement tools particularly when constructing a Cause and Effect Diagram.
One core component of TQM is the principle of continuous improvement. Quality tools and techniques in DMAIC methodology In Table 2 a possible inclusion of 7QC tools These approaches are different and definitely in three methodologies is presented. Define measure analyze improve control.
If you want to improve business processes efficiency or productivity then the PDCA cycle can help. Continuous improvement is a method to make sure that your processes methods and practices are as efficient accurate and effective as possible. This cycle is often credited to Dr.
Kanban to help you visualize manage and optimize your workflows. Gemba walks to keep leaders and front-line workers on the same page. There are several process improvement methodologies out there.
Based on effecting most categories we select processes to improve. Histograms are sometimes confused with bar charts.
Histogram Clinical Excellence Commission
A Histogram is a vertical bar chart that depicts the distribution of a set of data.
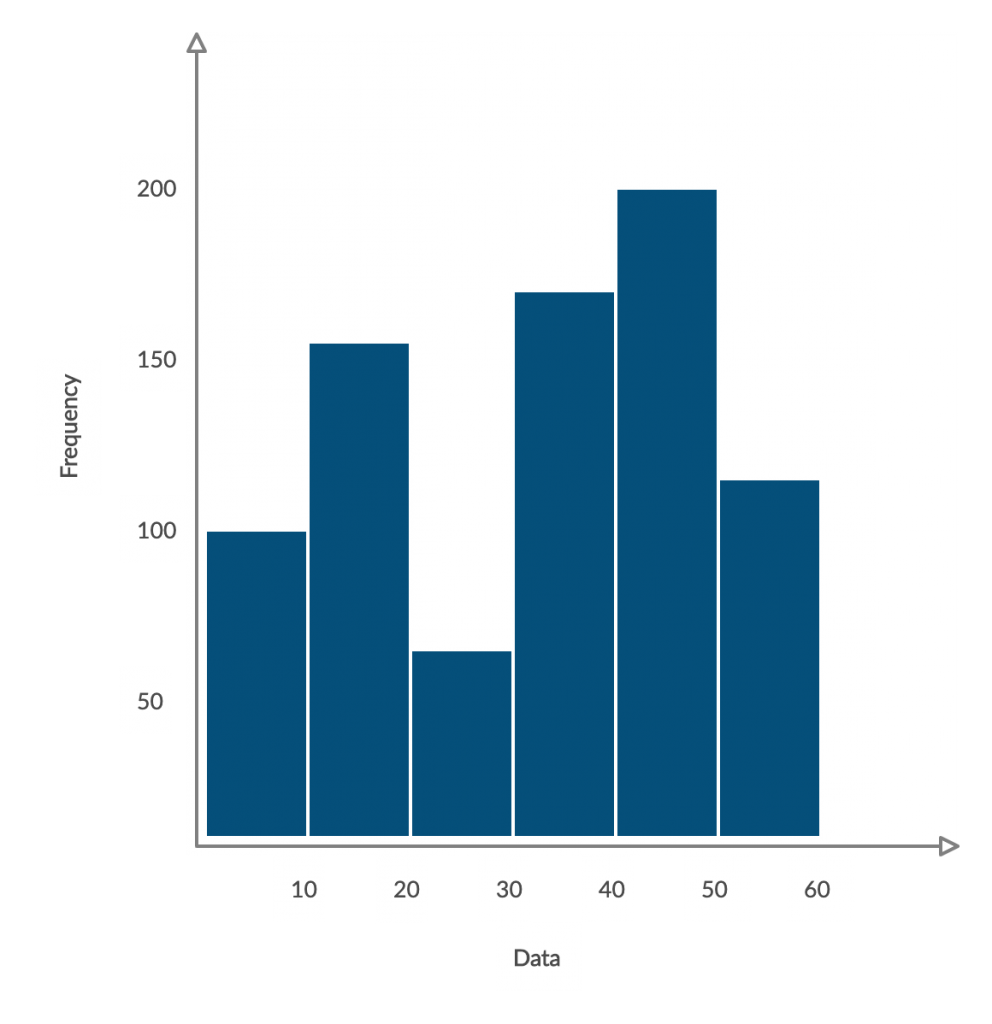
What is histogram used for by improvement teams. The Y axis is the frequency for that measurement. Quality tools can serve many purposes in problem solving. A histogram is a graphical display of data using bars of different heights.
Knowing how to translate histograms is an important tool in project management and project managers should use it to analyze their data. Contrast is defined as the difference in intensity between two objects in an image. A histogram is used for continuous data where the bins represent ranges of data while a bar chart is a plot of categorical variables.
These ranges of values are called classes or bins. The photo to the right shows data from a call center- specifically the time to answer an incoming call. And you decide what ranges to use.
Before creating a histogram be sure to read this discussion on data analysis. A histogram is a type of graph that has wide applications in statistics. They may be used to assist in decision making selecting quality improvement projects and in performing root cause analysis.
Histogram Quality Service Improvement and Redesign Tools. It is similar to a vertical bar graph. Histograms provide a visual interpretation of numerical data by indicating the number of data points that lie within a range of values.
Continuous data is part of six sigma. In a histogram each bar groups numbers into ranges. Histogram What is it.
It can also be used to determine acceptable limits as well as to determine which aspect of the project process should be further analyzed for improvement. Some authors recommend that bar charts have gaps between the rectangles to clarify the distinction. Histograms are necessary for continuous improvement measurements.
Taller bars show that more data falls in that range. A histogram displays the shape and spread of continuous sample data. The height of each bar shows how many fall into each range.
This chart shows how often each value occurs. The horizontal axis typically displays the measured value either a continuous numerical variable such as height distance or time or a discrete countable value such as number of items. In other words it provides a visual interpretation of numerical data by showing the number of data points that fall within a specified range of values called bins.
These Histogram examples are a graphical picture of data. And present data to management and your team. A histogram is a special type of bar chart used to display the variation in continuous data like time weight size or temperature.
They show your data distrubution before and after the improvement. The histogram is a graph that is often used in mathematics and statistics. Unlike Run Charts or Control Charts which are discussed in other modules a Histogram does not reflect process performance over time.
A histogram is a type of bar chart that displays a set of continuous data that you can use to evaluate the distribution or variation of data over a range for example weight length of time size and age. A histogram is a representation of frequency distribution. Histogram manipulation can be used for image enhancement.
It is the basis for numerous spatial domain processing techniques. Histogram refers to the visual presentation used for summarizing the discrete or the continuous data and the example of which includes the visual presentation on the graph the complaints of the customer made in the bank on the different parameters where the most reported reason of the complaint will have the highest height in the graph presented. In Plan Quality Management a Histogram serves as a preventive approach to improve processes.
Basic Tools for Process Improvement 2 HISTOGRAM What is a Histogram. The X axis is the measurement. This term is defined in the 5th edition of the PMBOK.
We use historical data to identify categories of causes effecting most. The histogram is one of the seven basic tools of quality control. A histogram can be constructed by segmenting the range of the data into equal sized bins also called segments groups or classes.
Height of Orange Trees. A histogram enables a team to recognize and analyze patterns in data that are not apparent simply by looking at a table of data or by finding the average or median. A histogram is used to summarize discrete or continuous data.
The histogram can help you represent frequency distribution of data clearly and concisely amongst different groups of a sample allowing you to quickly and easily identify areas of improvement within your processes. Histograms are used to measure how frequently values or value ranges appear in a set of data. For example if your data ranges from 11 to 18 you could have equal bins of 01 consisting of 1 to 11 12 to 13 13 to 14 and so on.
Histograms are a key process improvement tool. You measure the height of every tree in the orchard in centimeters cm. A histogram or frequency plot is commonly used to graphically view the distribution of your process data.
The frequency of the data that falls in each class is depicted by the use of a bar. Its helpful to think of a Histogram. They provide useful structure to brainstorming sessions for communicating information and for sharing ideas with a team.
Histograms provide one method to document your continuous improvement efforts. For example due to higher frequencies in IES MCC and EDR we may select improvements in Collect Requirement and. It is similar to a Bar Chart but a histogram groups numbers into ranges.
Popular Posts
-
By the end of the 1970s most of the factories in Japan were already using Total Quality Management TQM systems. According to the FDA report...
-
Multiple intelligences is the idea that there are many ways in which people learn. About This Quiz Worksheet. Multiple Intelligence Test ...
-
What Is an Itinerary. Are you going on a business travel. 13 Business Travel Itinerary Template Word Excle Pdf Free Premium Templates Be...
Featured Post
calico tortie cat
How To Spot The Difference Between Calico and Tortie Cats . Calico and tortoiseshell cats are best known for their beautiful multicolo...

ads
Pages
Power In Leadership
Search This Blog
Blog Archive
- January 2023 (3)
- August 2022 (4)
- July 2022 (23)
- June 2022 (29)
- May 2022 (37)
- April 2022 (20)
- March 2022 (20)
- February 2022 (21)
- January 2022 (28)
- December 2021 (36)
- November 2021 (22)
- October 2021 (31)
- September 2021 (26)
- August 2021 (37)
- July 2021 (33)
- June 2021 (28)
- May 2021 (26)
- April 2021 (28)
- March 2021 (46)
- February 2021 (24)
- January 2021 (39)
- December 2020 (40)
- November 2020 (29)
- October 2020 (22)
- September 2020 (31)
- August 2020 (24)
- July 2020 (37)
- June 2020 (33)
- May 2020 (34)
- April 2020 (32)
- March 2020 (41)
- February 2020 (21)
- January 2020 (41)
- December 2019 (40)
- November 2019 (32)
- October 2019 (34)
- September 2019 (42)
- August 2019 (30)
- July 2019 (39)
- June 2019 (26)
- May 2019 (29)
- April 2019 (37)
- March 2019 (40)
- February 2019 (43)
- January 2019 (30)
- December 2018 (35)
- November 2018 (28)
Labels
- 1800
- 1913
- 1939
- 1953
- 1959
- 1968
- 1969
- 1970
- 1987
- 2000
- 2012
- 2017
- 2018
- abbreviation
- abbreviations
- about
- above
- abraham
- absence
- accident
- according
- accords
- account
- accountabilities
- acorn
- acronym
- acronyms
- action
- activities
- activity
- actualization
- actually
- adairs
- adjectives
- adjustment
- adults
- advantage
- advertising
- affect
- affects
- after
- agenda
- ages
- agility
- agreement
- agreements
- aids
- aircraft
- albert
- alexander
- alliteration
- alpha
- alphabet
- alphabets
- also
- alternative
- anagram
- analyse
- analysis
- ancient
- angel
- animals
- announcement
- announcing
- another
- answer
- answers
- antonyms
- appeal
- appointment
- appraisal
- approach
- april
- archery
- area
- areas
- argumentation
- army
- around
- asking
- aspect
- assessment
- assessments
- attention
- attitude
- auditory
- auto
- awareness
- away
- awesome
- babies
- baby
- back
- balanced
- ball
- balls
- bank
- barnaby
- barrett
- based
- basic
- bass
- bear
- beard
- beautiful
- beauty
- before
- begin
- beginning
- behavioural
- being
- belong
- bene
- benefits
- benjamin
- best
- beta
- between
- bgfl
- biography
- biology
- birmingham
- black
- blake
- blame
- blanchard
- blanchards
- blarney
- bliss
- bloom
- blooms
- bloopers
- blow
- board
- body
- bolman
- bonding
- bonfire
- book
- books
- boomer
- born
- brand
- brazil
- breach
- break
- breakfast
- breathe
- briefing
- briggs
- brilliance
- bring
- british
- bruce
- bucket
- budget
- building
- business
- businessballs
- businesses
- cake
- calico
- call
- called
- calling
- cancer
- capital
- carol
- cartoon
- case
- catholic
- caused
- centi
- certain
- certificate
- certify
- challenge
- challenging
- change
- chapter
- character
- characteristics
- characterization
- charismatic
- chart
- chest
- chiefly
- child
- childrens
- choice
- christian
- christmas
- cited
- claim
- claims
- clarification
- class
- clean
- clever
- cliche
- client
- clients
- clips
- closing
- clothing
- clue
- clutch
- coaching
- cockney
- code
- cold
- comments
- common
- communicate
- communication
- company
- comparative
- compare
- competence
- competition
- competitive
- complain
- complaint
- complaints
- complex
- components
- concept
- concern
- conclusion
- confidence
- conformity
- confusion
- connected
- constructing
- constructive
- consulting
- contacts
- contemporary
- context
- contingency
- continuous
- contract
- contracting
- contrast
- contribute
- control
- conundrum
- core
- corn
- corporate
- correct
- corresponding
- cost
- courses
- covey
- cracker
- cream
- create
- crisis
- critical
- crossword
- crown
- cultural
- culture
- cure
- currency
- current
- cuss
- custom
- customer
- customers
- cutting
- cycle
- cycles
- dance
- dancer
- dancers
- dancing
- daniel
- data
- database
- date
- dating
- david
- dead
- death
- debris
- deci
- decision
- decisions
- define
- definition
- degrees
- delegate
- delegation
- demographics
- department
- derived
- describe
- describing
- description
- descriptions
- desiderata
- detail
- developed
- development
- devil
- diagnostic
- diagram
- dictionary
- difference
- different
- differentiation
- difficult
- dimensional
- direct
- directions
- director
- dirty
- disadvantages
- disaster
- disbelief
- discount
- discover
- discussed
- dismissal
- ditloid
- divert
- document
- does
- double
- doubt
- douglas
- download
- draft
- drama
- drink
- drop
- duck
- duke
- during
- dust
- duties
- dysfunctions
- earth
- economists
- education
- effect
- effective
- effectively
- efficient
- ehrmann
- eight
- elements
- elizabeth
- emotional
- employed
- employee
- employees
- employer
- employment
- encouraging
- energizer
- engineer
- english
- enhancement
- entendre
- environment
- epitaph
- epithet
- erickson
- erik
- erikson
- eriksons
- escalation
- especially
- essay
- ethical
- ethics
- evaluation
- events
- every
- everything
- evolution
- example
- examples
- excel
- excellence
- exemplary
- exercise
- exercises
- existing
- exit
- expectancy
- explain
- explains
- explanation
- export
- express
- expressing
- expression
- eyes
- fables
- factor
- factors
- family
- famous
- fear
- features
- federal
- feedback
- fell
- female
- fiedler
- figurative
- finance
- financial
- find
- finder
- fingers
- fired
- first
- fish
- fisher
- five
- flaming
- flight
- flint
- flirtatious
- flow
- foil
- folds
- following
- football
- forces
- form
- formal
- format
- forming
- fortunes
- four
- frames
- framework
- framing
- franklin
- free
- french
- freuds
- from
- front
- full
- funny
- game
- games
- gardner
- gardners
- general
- generation
- generations
- generic
- gerry
- gerund
- gestures
- gift
- giga
- giles
- give
- giving
- glass
- glossary
- goal
- golden
- goleman
- golf
- good
- governance
- government
- governmental
- graham
- grain
- grammar
- grammatical
- graph
- grass
- grave
- great
- greater
- greek
- grid
- grief
- grieving
- group
- groups
- grow
- guess
- guest
- guide
- guidelines
- gurus
- habits
- half
- hand
- handed
- handwriting
- handys
- hard
- harold
- have
- head
- health
- healthy
- heroes
- hersey
- herzberg
- herzbergs
- hierarchy
- higher
- highly
- hindi
- history
- homonym
- horse
- hospital
- hours
- house
- houses
- howard
- human
- humphrey
- hundredth
- icebreaker
- icebreakers
- iconic
- idea
- ideas
- identifies
- illustrate
- illustrated
- images
- impact
- implied
- importance
- important
- improve
- improvement
- include
- includes
- including
- indicator
- individual
- induction
- information
- infrastructure
- inquiry
- inspire
- instant
- instructions
- insurance
- integrity
- intelligence
- intelligences
- interest
- interesting
- internal
- interpersonal
- intimacy
- introducing
- introduction
- invoicing
- iowa
- ireland
- iron
- island
- isolation
- italiano
- itinerary
- jacob
- jacobs
- jamaica
- johari
- john
- johnson
- joke
- jokes
- joseph
- juxtaposition
- keep
- kenneth
- kids
- kinesics
- kinesthetic
- kingdom
- kipling
- kirkpatrick
- knackers
- knights
- knowledge
- koala
- kolb
- kolbs
- kotter
- kotters
- kouzes
- kubler
- lady
- lama
- landlord
- language
- languages
- large
- lateral
- latin
- layoff
- leader
- leadership
- leading
- learn
- learning
- left
- legal
- letter
- letters
- level
- levels
- libera
- life
- lifelong
- lifestyle
- light
- like
- likely
- likert
- limits
- line
- liners
- link
- lippitt
- list
- literal
- literary
- literature
- live
- local
- london
- longer
- longest
- love
- lowry
- luft
- luis
- magic
- main
- maintaining
- maintenance
- make
- makes
- making
- manage
- management
- manager
- managerial
- managers
- managing
- many
- market
- marketing
- mary
- maslow
- maslows
- mass
- material
- math
- mathematics
- matrix
- mcclelland
- mcgregor
- mcgregors
- mcquaig
- mean
- meaning
- meanings
- means
- measurement
- measuring
- mechanics
- media
- meet
- meeting
- meetings
- mega
- mental
- methods
- metric
- michael
- microsoft
- miguel
- military
- millennials
- miller
- million
- mind
- minute
- misconduct
- model
- modeling
- models
- modern
- mojo
- money
- monitor
- monkey
- monthly
- moolah
- moral
- more
- motivate
- motivation
- motivational
- motivator
- motorola
- mouton
- moves
- movie
- much
- multiple
- mumford
- murder
- mustard
- myers
- mythical
- nails
- name
- names
- nano
- narcissist
- nato
- need
- needed
- needs
- networking
- next
- nickname
- night
- nonverbal
- norming
- note
- notice
- number
- numbers
- objective
- objectives
- offer
- office
- officer
- olympic
- olympics
- omitted
- omni
- online
- operations
- operator
- opportunities
- opposite
- options
- orchestra
- order
- organisation
- organisational
- organisations
- organising
- organization
- organizational
- origin
- other
- outcomes
- over
- overview
- owner
- oxymoron
- packs
- palindrome
- paparazzi
- paper
- paradise
- parody
- part
- parties
- partnership
- passing
- path
- penny
- people
- perform
- performance
- performing
- period
- person
- personal
- personality
- perspective
- pestle
- peta
- phase
- phases
- philosophies
- phone
- phonetic
- phrase
- phrases
- physics
- picture
- pictures
- pigs
- pilot
- pink
- placidly
- plan
- planner
- planning
- play
- please
- poem
- poems
- point
- police
- policy
- poor
- porter
- porters
- positively
- posner
- postcode
- poster
- posture
- potential
- power
- practice
- practices
- prayer
- prefix
- prefixes
- presentation
- presentations
- presenting
- pressure
- principle
- principles
- printable
- problem
- problems
- procedures
- process
- product
- professional
- professionals
- profile
- profiling
- programmes
- programs
- project
- projects
- promotion
- pronouns
- pronunciation
- proposal
- props
- pros
- prospective
- provider
- psychological
- psychosocial
- public
- puns
- purpose
- puzzle
- puzzles
- pyramid
- quality
- questionnaire
- questions
- quick
- quiet
- quiz
- quizzes
- quotes
- random
- range
- rating
- raven
- ravens
- real
- recommendation
- redundancy
- refer
- reference
- refers
- reflective
- reflexive
- regarding
- registration
- regulations
- related
- relationship
- relationships
- relief
- relievers
- remove
- rensis
- reply
- report
- request
- required
- resale
- research
- resignation
- resolution
- resource
- resources
- respect
- response
- responses
- responsibilities
- responsibility
- resume
- retail
- retards
- review
- rhyme
- rhymes
- rhyming
- riddles
- right
- risk
- rocks
- role
- roles
- roman
- root
- ross
- round
- rudyard
- ruiz
- rules
- sack
- safeguarding
- safety
- salary
- sale
- sales
- salt
- same
- sample
- samples
- sarcastic
- satisfaction
- savings
- sayings
- scope
- score
- scorecard
- scoring
- sealed
- select
- self
- sell
- seller
- senior
- seniors
- sentence
- sentences
- service
- services
- several
- shared
- sheet
- shilling
- shirt
- short
- show
- shows
- sigma
- sign
- significance
- signing
- signs
- simple
- single
- sings
- site
- situation
- situational
- situations
- skill
- skills
- slang
- slide
- slight
- small
- smart
- social
- socially
- society
- socioemotional
- soft
- softly
- solve
- solving
- some
- song
- songs
- sound
- spanish
- speaking
- special
- speech
- spell
- spelling
- spin
- spoiled
- spoken
- spring
- staff
- stage
- stages
- stand
- standard
- stands
- start
- startup
- statement
- steps
- stick
- stop
- stories
- storm
- storming
- story
- strategic
- strategies
- strategy
- strength
- strengths
- stress
- strong
- structure
- student
- students
- study
- stupid
- style
- styles
- successful
- suggestion
- suitability
- suitable
- summary
- supplier
- survey
- sustainability
- swot
- syllogism
- symbol
- symbols
- syndicate
- synonym
- synonymous
- synonyms
- syntax
- system
- systems
- table
- take
- target
- task
- taxonomy
- tchaikovsky
- teach
- teachers
- teaching
- team
- teams
- techniques
- technology
- template
- templates
- temporary
- tend
- tender
- term
- termination
- terms
- test
- testimonial
- text
- that
- their
- them
- theme
- theories
- theory
- therapy
- thing
- things
- thinking
- thirst
- this
- threats
- three
- time
- timeline
- tips
- title
- titles
- tobacco
- today
- told
- toltèques
- tongue
- tools
- topics
- tortie
- total
- touch
- tour
- trade
- traffic
- train
- training
- trait
- transactional
- transformational
- translate
- translation
- travel
- triangle
- tricks
- triumph
- trivia
- trust
- truth
- tuckmans
- tune
- tutorial
- type
- types
- typical
- unconscious
- under
- unique
- university
- upon
- upper
- upside
- urban
- used
- uses
- utilitarian
- valence
- value
- variety
- vark
- veil
- verb
- verbal
- verification
- version
- versus
- very
- video
- view
- visual
- vocabulary
- wanna
- watch
- weakest
- weakness
- wedding
- weep
- welcome
- welfare
- wellbeing
- western
- what
- whats
- when
- where
- which
- whisper
- white
- wide
- widening
- wiki
- wikipedia
- will
- window
- winter
- wisdom
- with
- withdrawal
- within
- woman
- women
- word
- words
- work
- worker
- working
- workplace
- would
- write
- writing
- written
- year
- years
- yotta
- your
- zeros
- zetta
- zumba